Containers Plant
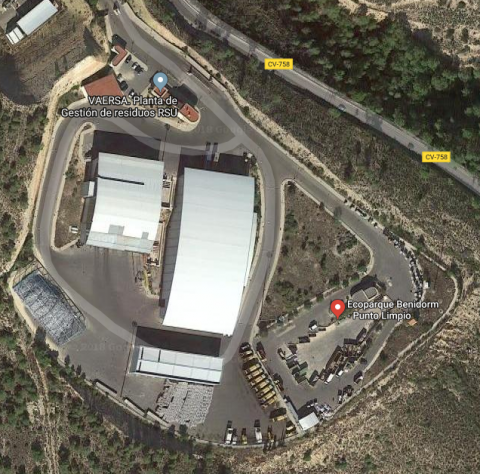
The plant is located at the northern end of the theme park reserve area, next to the municipal solid waste transfer plant and the eco-park.
The waste comes from the yellow container, where containers, cans and plastic waste are deposited, among which we can find:
Cans
Aerosol sprays
aluminium trays
Beer Barrel
Tapas
Wrappers
Bricks
plastic trays
Boats
toothpaste tubes
Bottles
food box
food packages
fruit crates
wine corks
It accommodates containers and waste generated in 52 towns in the area of influence of Benidorm: Adsubia, Alcalalí, Alfaz del Pi, Altea, Beniardá, Beniarrés, Benichembla, Benidoleig, Benidorm, Benifato, Benimantell, Benimeli, Benissa, Benitachell, Bolulla, Calp, Callosa, Castells, Confriedes, Denia, Els Poblets, Finestrat, Gata, Guadalest, Xaló, La Nucía, La Vila, Lliber, Murla, Ondara, Orba, Orxeta, Parcent, Pedreguer, Pego, Polop, Rafol, Relleu, Sagra, Sanet i Negrals, Sella, Senitja, Tárbena, Teulada, Tibi, Tormos, Vall de Alcala, Vall de Ebo, Vall de Gallinera, Vall de Lagurart, Vergel, Xabia, (ZONE XV Zonal Waste Plan of the Valencian Community ).
Plant characteristics:
- Plot with an area of 45,412.83 m2, but with an affected area of 69,119.93 m2.
The plot on which the building will be carried out is within the Special Master Plan for uses and infrastructure of the Terra Mítica Theme Park, qualified as NNPI2, Non-Developable Land Protected by Infrastructure.
The packaging plant is made up of two united elements: the packaging warehouse (rectangular of 3,649.94 m2) and the visiting area of the warehouse.
The building is formed by a nave with two walls. An upper one, with 6 accesses for recycling collection trucks and a lower one, with 5 accesses for trucks transporting selected products.
On the upper level is the unloading area for products intended for recycling, coming from the “igloo” packaging containers (yellow container), with an area of 683.6 m2.
Products to recover:
- Paper/cardboard
plastic film
High-density polyethene
Plastic mix
PVC
PET
Treatment Process:
1. Trucks are weighed at the entrance and exit of the Waste Center
2. Once the load weight of the truck is controlled, they unload at the unloading yard.
3. Bulky materials are separated at the discharge bay to prevent them from entering the treatment line.
4. Once the waste enters the line, the bags are torn apart for subsequent classification.
5. Waste separation by size, separation trommel.
6. Manual separation of plastics, paper, cardboard, bottles, wood, etc.
7. Pneumatic separation of film plastics, with a compaction press.
8. Magnetic and electrostatic separation.
9. Separation of magnetic composition part products, such as tetra bricks.
10. Adaptation of products in compacted bales.
11. Adaptation of the rejected product in the form of bales, for subsequent transfer to a treatment centre.
The waste classified by size passes onto conveyor belts, of which in three of them, manual selection is carried out by operators on both sides of the belts; Once the manual selection has been carried out, the magnetic and electrostatic separation of the metallic and/or quasi-metallic products is carried out.
All recyclable or non-recyclable products are arranged in the form of bales for subsequent transport to the treatment centres.
The warehouse has electric fans that carry out permanent air renewal, which through the appropriate ducts send the stale air to biological filters to avoid producing odors outside.
The starting point is a quantitative estimate of 10,000 MT/year of light packaging.
Regarding qualitative composition (% by weight of each component), the following average values have been estimated:
Paper/cardboard: 10%
Brik: 9%
Steel: 12%
Aluminum: 2%
PE-AD: 10%
PE-BD: 9%
PVC: 2%
PET: 9%
Film:11%
Mixed plastics: 5.5%
Others: 20.5%
Plant functioning:
- Working day of 40 hours per week, from Monday to Friday, in a single work shift.
Daily capacity: 38.46 T/day.
Hourly capacity: 4.8 T/hour